INTERGEN COGENERATION FOR THE BEST ITALIAN DELICACIES
Igor, the worldwide leader in the production of Gorgonzola, has chosen the energy division of the IML Group to implement its energy efficiency strategy
Lomagna (Lecco), July 2016 – Igor, an Italian gourmet company, known throughout the world for its production of the famous Gorgonzola D.O.P. cheese, chose Intergen as its strategic partner to implement its energy saving and sustainability policy be installing a 2MWe cogeneration plant.
An Italian company founded by the Leonardi family, Igor is always searching for process innovation and wholesome ingredients to ensure the long-lasting quality of the Gorgonzola it exports around the world. The company is headquartered in Cameri (Novara) and in recent years it has built various extensions to the plant which have contributed to increasing the total area from 35,000 to 50,000 square meters. The expansion of the production site and the increasing demand for heat and electricity, led the company to undertake an efficiency programme with the installation of a cogeneration plant designed, assembled and commissioned by Intergen, an Italian company with premises in Lomagna (Lecco) and a leader in the energy sector.
The desire to adopt a cogeneration unit reflects Igor’s need, like many other companies in the food industry, to optimise its production process, which requires the simultaneous use of electricity and heat. The installed plant provides a concrete answer to the need to self-produce energy carriers used in the processes and to reduce CO2 emissions to a minimum. The cogenerator, along with the implementation of other cutting edge technologies, contributes to making the processes of the Cameri plant among the most modern and efficient in its market.
Following an accurate analysis of the plant’s consumption, Intergen designed and installed a custom cogeneration plant equipped with MWM (Motoren Werke Mannheim)
TCG 2020V20 (250 NOx) engine fuelled by natural gas, one of the best performing on the market. The MMW engines, distributed by Intergen in Italy since 1987, are the vibrant core of the cogeneration systems and represent a certainty in terms of reliability and efficiency. In addition to being top performing in terms of electricity efficiency, they are known for the thermal energy they produce, since the temperature of the exhaust generated by 250 NOx is equal to 419°C (50°C higher than other brand engines with the same power).
The electricity produced by the Igor cogenerator (2,000 kWe) will be entirely consumed by the plant’s utilities. From a heat viewpoint, the hot water supplied by the engine will be accumulated within an additional tank, thus increasing the availability for plant uses and partly replacing the hot water produced by traditional means. The steam generated by the exhaust will be conveyed and used to partly cover the production of steam with traditional boilers.
The cogeneration plant, in a soundproofed container, was installed inside an existing service building and will guarantee an electricity efficiency of 42.4% and heat of 44.4%, for a total efficiency of 86.4%. This set-up will produce a significant economic savings compared to a traditional supply system, ensuring a pay back of the investment in a very short time frame. The reliability of the German MWM engines and the design logic of the plant will also make it possible for island operation of the plant, guaranteeing an uninterrupted supply and maximum efficiency of the production cycle.
Intergen will assist Igor during the post-installation phase to ensure the best operation of the cogenerator thanks to a Full Service programme available 7 days a week, 365 days a year. In addition we will provide a remote supervision system that is able to acquire all of the parameters useful for optimising the plant including High-Efficiency Cogeneration.
The technical specifications of the Intergen cogeneration plant are provided below. It is equipped with a natural gas fuelled MWM TCG 2020V20 (250 NOx) engine and installed at the Igor plant:
LHV (Lower heating value) of Natural Gas | kWh/Nm3 | 10.10 |
Natural gas consumption | Nm3/h | 467.4 |
Steam pressure | oC | 12 barg |
Input energy | kWt | 4,721 |
Electrical power | kWe | 2,000 |
Thermal input in hot water | kWt | 1,202 |
Thermal input in steam | kW | 882 |
Electrical efficiency | % | 42.4 |
Thermal efficiency | % | 44.4 |
Total efficiency | % | 86.8 |
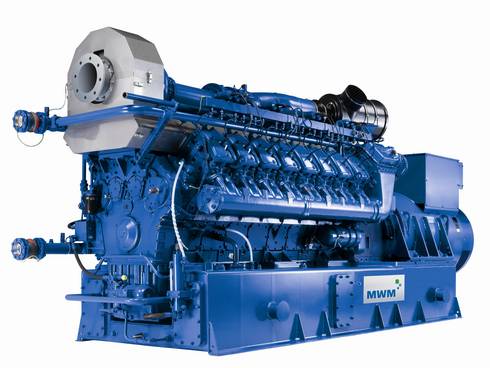